STONEWARE
View all related objects in the collections
Many questions remain unanswered about aspects of stoneware production in Mainland Southeast Asia in the past, concerning technical procedures as well as social organization, economic structure, marketing, and aesthetic appreciation. Stoneware production has largely disappeared from once flourishing centers such as the former Angkor and Lan Na kingdoms. Ethnographic studies of recent or present-day production in the region are suggestive of practices followed in the past, and future scientific and archaeological studies may clarify uncertainties about materials processing or workshop organization.
Source
Stoneware clay is excavated from mines dug deep to reach and follow veins of specialized clay. The disappearance of a source (because it was depleted or, in recent years, flooded by a dam) was reason for a village manufacturing stoneware on a small scale to discontinue production. Large established centers—such as Bat Trang near Hanoi in North Vietnam—were able to buy clay from greater distances and have it delivered by riverboat or, now, by truck. Clay mining became a specialized occupation to support such centers.
Processing
Stoneware clay is usually stored outside near the workshop to allow for weathering. Some workshops prepare their clay bodies by mixing two clays with different properties. In preparation for use, the clays are soaked in water separately, then mixed by measure before being kneaded by foot (or by an electric pug mill).
Making stoneware
Today teams of two people collaborate to make stoneware in many locations, a practice that was probably common in the past as well. The potter ("shaper" in Northeast Thai-Lao terminology) uses coils of clay to build the vessel on a small, solid wooden wheel set on a pivot embedded in the ground. His assistant (the "spinner") prepares the coils and spins the wheel while the potter finishes and smoothes the coiled form with a pair of wooden blades. In workshops in North and coastal Central Vietnam, where many women make stoneware, and at Chinese-influenced kilns in Central Thailand, the potter squats at a low wheel while the assistant stands to spin the wheel by foot.
Glazing—or not
Glaze—especially when combined with forms of carved or painted decoration, or when applied to small, portable forms such as dishes, bottles, and covered boxes—has been the focal point of much study of Southeast Asian ceramics. Applying painted decoration and glaze to stoneware and firing it successfully took special tools and skills.
Throughout the region, however, much stoneware was made without glaze, although it sometimes bears a coating of melted wood ash (fly ash) that landed on the vessel during firing. Some pottery communities (such as Ban Bang Pun in Central Thailand) made only unglazed stoneware. Early kilns in the Angkor region, such as those at Tani, fired both glazed and unglazed wares in the same structure. Larger centers such as Sawankhalok or the Red River Delta potteries in North Vietnam produced both glazed and unglazed wares, with some kilns specializing in glazed wares and others firing unglazed wares.
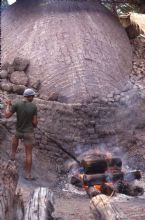
A potter fires stoneware jars in a wood-fired crossdraft kiln. Ban Pon Bok, Nong Khai province, Northeast Thailand, 1990. Photograph by Louise Cort.
Firing
In Northeast Thailand today, all teams of potters in a community share the work of building and maintaining the kilns necessary for firing stoneware. Each team operates the kiln in rotation to fire its own products, using wood as fuel. In the past, kilns were often situated along riverbanks within easy reach of the boats used to take wares to market, although pickup trucks have now replaced boats.
Using stoneware
Until the introduction of glass, metal, and plastic, stoneware vessels served as universal containers. Small jars (with stoppers of wood, paper, or leaves) held tea, salt, or cooking sauces. Large jars were indispensable for storage of rice and water or of precious possessions such as textiles. Large jars were also used to brew and serve beer made from cooked rice fermented with yeast. The beer, which was thinned with water and drunk from the jars using long straws, played an important role in customs of hospitality and religious ritual.
Some jars, such as the thick-walled bottles made at the San Kamphaeng kilns in North Thailand or the cylindrical jars from the My Xuyen kilns in Central Vietnam, probably transported specific, though as yet unknown, commercial products. Large jars were used and reused as containers for shipboard supplies or trade goods, and are sometimes excavated from shipwrecks full of small ceramic objects. The standardized sizes of such jars were probably universally understood as measures of volume.
Containers for lime paste—made from burned shells and wrapped with areca nuts in betel leaves to make betel quid, a stimulant and emblem of hospitality—were essential elements of social life in the region, and their varied shapes reflect the tastes of different cultural groups. In Cambodian culture, the lime-paste pot is named for the ak, a bird said to cry for its absent mate, and Angkor-period pots often took the bird's form (sometimes misidentified as an owl).
Durable stoneware vessels also served ritual purposes. For example, gourd-shaped bottles with human features may have been used for pouring water during rituals. Lotus motifs adorn the lids of containers that were possibly intended to hold cremated remains. Remains were also buried in jars on the grounds of Buddhist monasteries. Vessels in the form of a stupa (burial mound of the Buddha) housed small Buddhist images. Finials adorned roofs of monastery buildings. Small sculptures of humans and animals may have been offered at "spirit houses" to honor the lord of the land, or they may have been used in ritual practices.
Related:
Luu Hung article in Library
Don Hein article in Library
Stanley O’Connor article in Library
Video of potters making and firing stoneware jars and mortars in Ban Pok Bok, Nong Khai province, Northeast Thailand, http://www.asia.si.edu/explore/seasia/hauge-ceramics/