EARTHENWARE
View all related objects in the collections
Little study has been done of historical earthenware production in Mainland Southeast Asia. The traces left by earthenware processing are modest, especially if no kiln is involved, and can easily be overlooked in an archaeological context. The earthenware production center of Otein Taung ("pottery hill") on the outskirts of Pagan in Upper Burma (Myanmar) may be the first to be identified and studied. It operated from the ninth through the fourteenth centuries, producing two large mounds of debris at the sites where firings were conducted (Hudson 2004). While we await further discoveries of this kind, ethnographic studies of present-day village-based earthenware production and scientific analysis of prehistoric earthenware offer suggestions for processes used in the intermediate past.
Source
Earthenware clay is typically dug from a vein close by the potter's village. On the simplest scale, a lone woman may dig enough clay in the morning to carry home in a pair of baskets on a shoulder-pole and use it to prepare ten pots that same day. When work continues on a regular basis, clay is dug periodically in larger quantities and stored at the potter's house, with sufficient material for the next day's use prepared each evening.
Processing
The clay is wetted with water (or sometimes soaked overnight) and then kneaded to an even consistency to remove stones and other impurities and to mix in additives such as sand, rice chaff, or prepared temper. Temper is prepared today by some lineages of potters in Northeast Thailand (Cort and Lefferts 2000) and Cambodia (Mourer 1986) by mixing wet clay with large amounts of rice husks, forming the mixture into balls, firing them, and pulverizing them into powder. A similar additive has been identified in some prehistoric earthenware made in Northeast Thailand (Vincent 1988). These additives reduce the plasticity of the clay and make it more suitable to the shaping methods and to firing in an open bonfire. Kneading may be done by hand in a woven bamboo basket for small quantities or by foot in a shallow pit or on a buffalo hide (or plastic tarpaulin) for larger amounts.
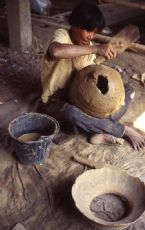
A potter uses paddle and anvil to shape a water jar. Ban Wang Tua, Khon Kaen province, Northeast Thailand, 1994. Photograph by Louise Cort.
Shaping
Women potters making earthenware in Southeast Asia use a minimal kit of tools, but their techniques are neither simple nor primitive. Their skilled hands and effective use of tools indicate mastery of knowledge passed from one generation to the next.
Mistaken descriptions of the process for making a round-bottomed pot have resulted from erroneous extrapolation from stoneware processes (for example, Green, Harper and Intakosi 1987, 78-79). Earthenware potters first make the vessel mouth and rim on a preliminary form, then shape and finish the body (Cort, Lefferts, and Reith 1997). The preliminary form is distinctive to, and diagnostic of, each cultural lineage of production, and the numerous variations of this form include hollowed-out solid cylinders, cylinders formed from clay slabs, and cylinders constructed on flat bases from clay coils or rings. In most cases potters revolve around the preform, which rests on a wooden post or similar support of appropriate height, but some lineages of potters use a revolving wheel (Lefferts and Cort 2003).
Tool kits for finishing earthenware vary among cultural groups. For shaping, most potters employ a set consisting of a wooden paddle and an anvil made of river pebbles or fired clay. To produce the final form, they strike the paddle against the soft wall of the preform, which is supported by the anvil held inside. This stage includes closing the open base or rounding the flat base of the vessel. Some communities of potters use bamboo or metal rings to scrape the clay to its desired thickness and shape, which includes rounding the preliminary flat base.
Paddles may also impart texture, which makes the pot both attractive and easier to handle. Early potters often wrapped their paddles with twisted cords of varying coarseness. More recent potters used paddles carved with patterns, or they produced a smooth surface by using a plain paddle, then added motifs around the neck with a carved paddle or individual stamps. Some applied colored mineral pigment before firing.
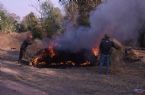
A potter and her husband fire water jars. Ban Wang Tua, Khon Kaen province, Northeast Thailand, 1994. Photograph by Louise Cort.
Firing
After thorough drying, and with careful choice of weather and time of day, the pots are ready to be fired. In the open-hearth firing that is most common, potters carefully construct a platform from several layers of branches or bamboo stalks, arrange the pots on the platform in rows or short stacks, and cover them with rice straw. Once the fire is lit, the process moves rapidly, and the potters keep watch for areas requiring additional fuel. The typical firing is complete in less that an hour. In some areas, potters construct low permanent walls to shape the firing space (Reith 2003; Mourer 1984); some potters employ updraft kilns (Katz 1991).
The color of fired earthenware ranges from white to red to black, depending on the raw materials and firing process used. The bonfire may leave dark carbon smudges where flame directly touched the vessel. An intentionally smoky firing deposits carbon on the pot to blacken it and make it less porous. Some potters coat fired pots with plant resin for the same purpose.
A matter of function
A variation of earthenware can be made by intentionally underfiring stoneware clay, in which case it remains porous and functions as earthenware. Some villages making stoneware along the Mekong River in Laos also fire this type of "earthenware" in the spaces at the rear of their kilns where the temperature is not sufficient for stoneware. Apparently potters at the Maenam Noi kilns in Singburi province, Central Thailand, used the "cool" spaces within their massive crossdraft kilns in the same manner. Creating products that could sell readily as earthenware was probably preferable to producing undesirable underfired "stoneware" jars.
Earthenware potters sometimes use locally available stoneware clay to make "earthenware." Testing showed this to be case in Kompong Chhnang, Cambodia, where potters dig one type of clay from a nearby mountain to mix with clay from the fields. A sample of the mountain clay was fired successfully to stoneware temperature (Scott Meredith, pers. comm.).
Using earthenware
Potters in Southeast Asia shaped earthenware clay into myriad forms. Versatile, round-bottomed cooking pots, which rest securely on three stones arranged in the hearth or on three-pronged earthenware stoves, could also be used to simmer herbal medicine, steep dyes for textiles, or bury cremated remains. Round-bottomed pots were also employed to fetch water and to chill it for drinking, using the porous vessel's property of evaporation. Sometimes water-cooling vessels were provided with a ring-shaped foot for stability. In the absence of such a foot, it is not always easy to guess the likely use of a round pot.
Other forms served more specific purposes. A Buddhist monk, for example, might carry a clay alms bowl instead of a metal one to receive food offerings. Meanings and uses of some earthenware objects are still ambiguous. Small figures of people and animals may have been placed in "spirit houses" (shrines to guardians of the land) or may have served as game pieces.
Related:
Video of a potter making and firing earthenware pots in Ban Cham Saming, Sisaket province, Northeast Thailand, http://www.asia.si.edu/explore/seasia/hauge-ceramics/